FEATURE
St. Petersburg College’s Innovation Lab: How We Built a 3D Printer … Almost
by Chad Mairn and Joushua Stein
Libraries offering 3D printing can help show people that simple design ideas can change the world. |
3D printing is not new; in fact, Chuck Hull invented stereolithography (i.e., solid imaging) in the mid-1980s. However, it does seem that 3D printing has started to take over the world, especially since printers are now affordable for many consumers. 3Dprinted cars, homes, prosthetic limbs, circuit boards, food models, tools, and almost anything else imaginable are now mainstream. Moreover, society is seeing new and innovative 3D design and printing applications that help solve everyday problems and help make our lives better. In fact, the Innovation Lab, a collaborative space for emerging technologies inside the Seminole Community Library at St. Petersburg College, has helped students and public patrons 3D print a variety of prototypes such as replacement parts for common household appliances and nurse intercom holders.
Hot Off the Presses
A stunning example of the work coming out of our lab is a St. Petersburg College student’s medical capstone project. Tasked with finding a solution to a practical problem by using technology, one student decided to use 3D design and printing to create a nurse intercom holder for hospital beds. The intercom devices call nurses to the patient’s bed and control the TV, but they are dropped frequently, resulting in occasional injuries and other complications. The plan was to design an object that can be 3D printed to hold the intercom safely on the side of the patient’s bed. The prototype, tested in an actual hospital setting, was approved unanimously. Libraries offering 3D printing can help show people that simple design ideas can change the world.
Going further, the Innovation Lab is also working on two accessibility and tactile learning projects using 3D printing. The first project is dealing with visualizing geometric shapes and graphs for measurement, which can be challenging for students who are blind or have low vision. Students who prefer different learning styles often struggle with visualizing and subsequently understanding certain subjects such as mathematics and biology. Screen-reading technology does not address this issue, so our project was to digitally design and print 3D kits to help engage students with graphing and geometry by illustrating mathematics. The 3D math kits are manipulatives in that students can physically plot points and adjust graphing bars using 3Dprinted templates.
The other project is an attempt to fill a gap in tactile interaction and learning from histological images. Histology is the study of the microscopic structure of tissues. Since many students are unable to study tissues under a microscope, the plan was to create 3D objects from 2D histological images. Initial testing of these objects with blind students was done, useful feedback was gathered, and slight revisions are proceeding.
What Is 3D Printing?
3D printing starts with designing a 3D object using a computer-aided design (CAD) or 3D-modeling application. There are 3D scanners on the market that capture objects in 3D, but they usually need meshing (i.e., cleaning up, smoothing) before they can be 3D printed. Once the object is created, a file is exported that can then be read on a 3D-printing host application, such as Repetier. The most popular file type for 3D printing is a stereolithographic or standard tessellation language (.STL) file.
Fused deposition modeling (FDM) is a common printing process in which plastic filament feeds mechanically into an extruder that pulls the filament into a heater block that melts it. The heated filament oozes out of the nozzle head onto the heat bed and is printed layer by layer. These layers are created (i.e., sliced) by applications such as Slic3r and generate G-code, which will instruct the nozzle to print at the precise X, Y, and Z positions.
Our 3D Printer Is Self-Replicating
The Innovation Lab uses a Monolith 3D printer, built locally in St. Petersburg, Fla., by FreeFab 3D. This printer is a custom, open source device inspired by a RepRap design. RepRap (reprap.org) is “humanity’s first general-purpose self-replicating manufacturing machine.” In addition to RepRap printers, you can search for “Core XY” at thingiverse.com to find others. Many of the Monolith parts were 3D printed, so we decided to look into making our own 3D printer. To learn more about the
Monolith printer, visit freefab3d.com.
How Not to Replicate a 3D Printer
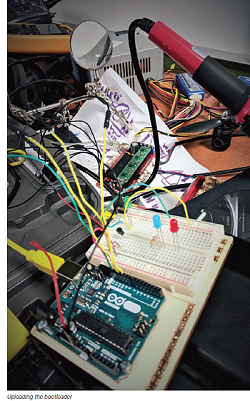 |
Uploading the bootloader |
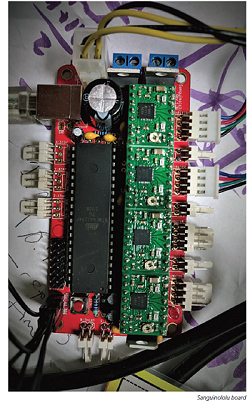 |
Sanguinololu board |
The Innovation Lab inherited a project from a volunteer, which was to build a RepRap Mendel printer. The RepRap is a partially self-replicating printer, so much of it can be 3D printed by other printers or another RepRap. It is open source, specifically available under the GNU General Public License. Detailed assembly instructions and 3D parts are available at reprap.org. The volunteer left an instruction manual, most of the actual 3D printer parts (i.e., 3D-printed components, motors, structure bars, and bolts), and what was originally believed to be a completed printer motherboard.
The first move was finding the 3D models for the parts of the Mendel. Several parts were missing or damaged, so we printed replacements on our Monolith. At this stage, not all of the non-3D printed parts for the printer were in the lab. It is a good idea to follow this advice: Fail as quickly as possible. It is better to take a small amount of time to know whether something is possible than to invest a lot of time and find out at the end it cannot be done. As it turned out, the manual did not have enough detail on certain parts required, especially for the extruder. The extruder heats and deposits the plastic. Building an extruder seemed difficult, so plans changed to build a 2D printer instead and attach a writing implement where the extruder would normally go. This redesign was unnecessary because more detailed specification on parts was available online.
There is a lesson to learn from this, seemingly in contrast to the previously mentioned advice: Do not give up too easily. As with many things in life, a balance must be struck. Do not waste time on a project that cannot be completed, but do the due diligence.
Moving On to the Guts
It was time to work on the software and computational hardware side of the printer. The volunteer left a Sanguinololu Rev 1.3a as a printer control board, with a 16MHz ATmega1284p microcontroller. Microcontrollers can have something called a bootloader that allows programs to be uploaded via USB. The first attempt to upload a 3D-printing Sanguinololu board firmware, Repetier, via USB failed. This suggested the board did not have a bootloader, so one was uploaded. You can use a device specifically made for programming bootloaders to do so, but it is also possible to use an Arduino. After another firmware upload attempt, the board was able to connect via a laptop to Repetier and to the printer. Even so, none of the motors on the printer moved when instructed to do so.
The Sanguinololu wiki recommended specific fuse settings for the microcontroller, and the board needed stepper motor drivers. Fuse settings are named as such because they were once real fuses: pieces of metal that could be burned out to permanently break a connection. Nowadays, these fuses are digital and can be read and written over as many times as you could practically desire. Fuses are the settings of the microcontroller. You could change whether the board uses an external or internal clock, how much time after a reset should be spent checking for communication from a programmer, and many other settings in the same vein. The wiki specified that the JTAG fuse must be disabled for the printer to work properly.
Generally, a motor does not operate at the same voltages and amperages a computer runs on, and this is the case with the Mendel printer. The stepper motors need a driver, which is controlled by the ATmega microcontroller and can handle the higher amperes the stepper motors require. It is like a relay; it allows a small voltage and current to control a greater voltage and current.
It took a while to find out that the stepper drivers were needed because it was assumed the board was completely assembled. There is another lesson to be had here: Learning a whole topic is often faster than searching for a specific answer. Even in this age when most answers can be found in milliseconds with search engines, a comprehensive knowledge of a topic should not be undervalued. Imagine if a doctor relied on the internet to know which medicine can cure an ailing patient. The fact that the medicine could interact negatively with another medicine would likely be missed. Having a complete knowledge also is useful for debugging purposes. Without knowing what to expect from something, how can one know if it is doing anything wrong? The final problem the printer had was the stepper drivers not being seated (i.e., plugged in) properly. If one had comprehensive knowledge of the printer, such a problem would be quickly solved with a voltmeter test.
Work in Progress
Right now, the printer is communicating with Repetier to move motors and the heat bed, but there is still work to do. The current plan is to convert 2D images into G-code to instruct the printer to draw a picture similar to the way Botsy—a portable drawing machine for quickly outlining artwork on horizontal and vertical surfaces—works. A flexible drawing implement mount will be created to allow printing on uneven surfaces. At the time of this writing, the RepRap wiki was updated to include detailed information regarding the extruder piece, so it is likely this printer will be dualpurpose: a 2D drawing machine and a 3D printer. If you would like to see the progress, check out our webpage at ilab-2d-printer.firebaseapp.com. Overall, taking on a project like this was, and will continue to be, a meaningful learning opportunity that has given a deep understanding and appreciation of how 3D printers are built. More importantly, though, it demonstrates what it takes to get them to function properly. 3D printers are complex machines that do phenomenal work and seem magical. The lesson—fail as quickly as possible—definitely applied throughout this project, but learning from failure is proof that one is trying.
|